The Vital Role of Plastic Injection Tooling in Modern Manufacturing
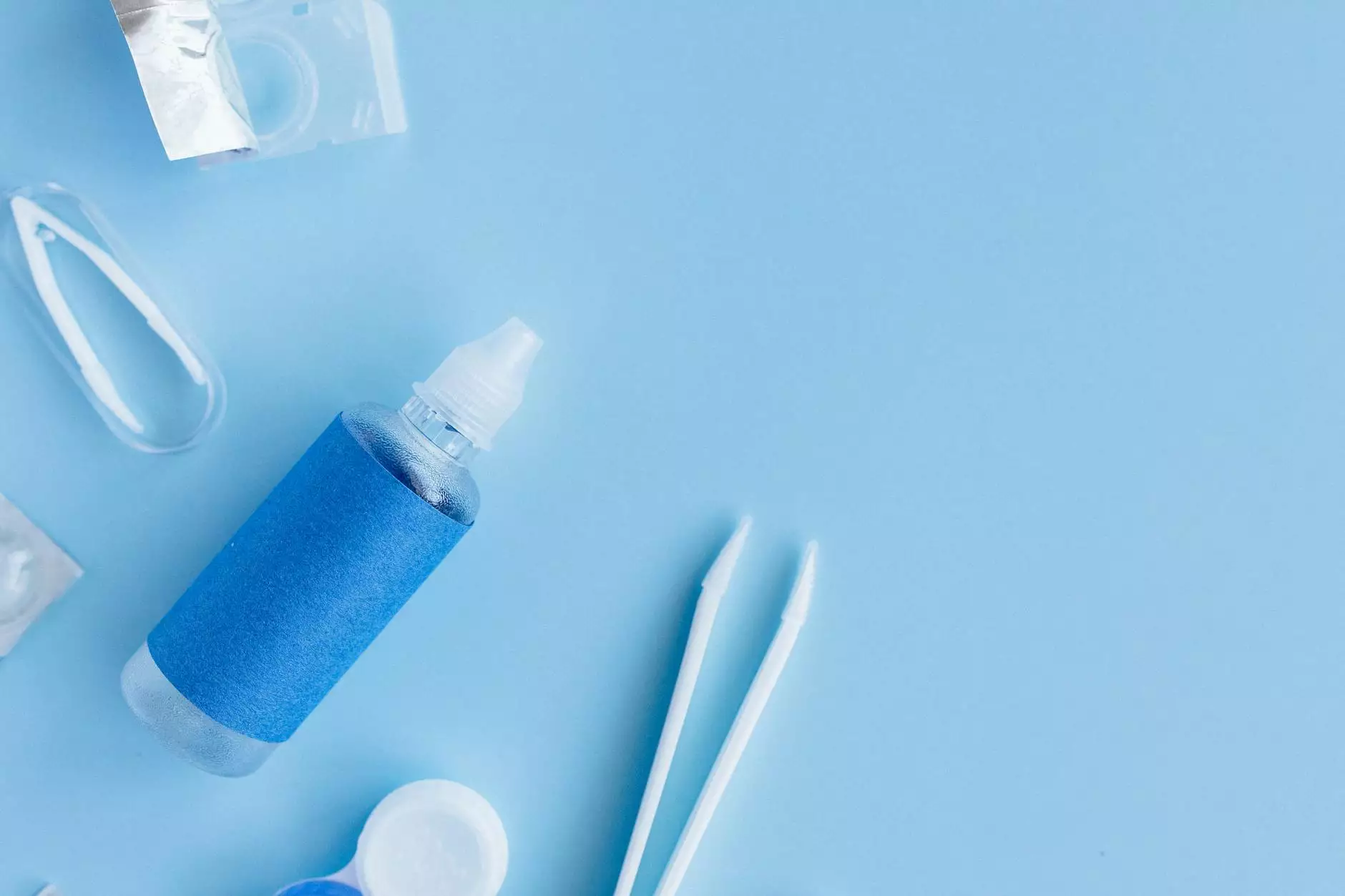
The landscape of manufacturing has evolved dramatically over the past few decades, largely due to advancements in technology and innovation. Among the various methodologies that have emerged, plastic injection tooling stands out as a pivotal process that significantly enhances product development and efficiency. This article delves deeply into the world of plastic injection tooling, exploring its benefits, applications, and the overarching impact it has on the business sector, particularly in the realm of DeepMould, a leader in metal fabrication and injection molding.
Understanding Plastic Injection Tooling
At its core, plastic injection tooling refers to the process of creating molds used in the manufacturing of plastic parts. This process allows for the rapid production of high-quality, consistent components tailored to specific requirements. The tooling involves several critical steps including design, material selection, manufacturing, and finishing. By utilizing these molds, businesses can produce intricate designs with remarkable precision and reduced lead times.
The Process of Plastic Injection Tooling
The process of plastic injection tooling can be broken down into several key stages:
- Designing the Mold: This is the initial phase where engineers and designers collaborate to create a mold that meets specific design requirements. Advanced software tools, such as CAD (Computer-Aided Design), are employed to visualize the mold and its components. During this stage, factors like material flow, cooling channels, and ejection systems are meticulously planned.
- Selecting Materials: The choice of materials for both the mold and the final product is crucial for ensuring quality. Common materials for molds include various steel grades and aluminum, chosen based on their durability and cost-effectiveness.
- Manufacturing the Mold: The actual construction of the mold utilizes precision machining techniques, including CNC (Computer Numerical Control) machining, which ensures that every detail is crafted to perfection.
- Testing and Optimization: Once the mold is built, it undergoes rigorous testing to identify any flaws. Adjustments are made as necessary to optimize the mold for production.
- Production Run: The final stage involves using the completed mold for mass production. The plastic is injected into the mold under high pressure, allowing it to take shape as it cools and solidifies.
Benefits of Plastic Injection Tooling
The advantages of plastic injection tooling are numerous, making it an invaluable technique for manufacturers across diverse industries. Here are some of the most significant benefits:
- High Efficiency: Once the molds have been created and optimized, the injection molding process allows for the rapid production of parts, significantly reducing time-to-market.
- Cost-Effectiveness: While the initial investment in tooling can be substantial, the long-term savings achieved through mass production often outweigh these costs.
- Design Flexibility: Plastic injection tooling enables intricate and complex designs that would be challenging to achieve with other manufacturing methods, allowing businesses to innovate effectively.
- Consistency and Quality: The precision of injection molding results in highly uniform products, ensuring that each component meets stringent quality standards.
- Material Versatility: A wide variety of plastics can be utilized, including thermoplastics and thermosetting plastics, enabling manufacturers to select the best material for their applications.
Applications of Plastic Injection Tooling
Plastic injection tooling is utilized in an array of applications, making it versatile across various sectors. Some notable applications include:
Automotive Industry
In the automotive industry, plastic injection tooling is used to produce a plethora of components including dashboards, bumpers, and other interior and exterior parts. The lightweight and durable nature of plastic parts contributes significantly to fuel efficiency and overall performance.
Consumer Products
From household items to electronics, consumer products benefit immensely from plastic injection tooling. Items such as toys, containers, and kitchenware are manufactured using this efficient process, ensuring affordability without compromising quality.
Medical Devices
The medical field demands precision and reliability, making plastic injection tooling ideal for manufacturing medical devices and components. Products like syringes, inhalers, and diagnostic tools are produced with stringent regulatory compliance, ensuring safety and efficacy.
How DeepMould Leverages Plastic Injection Tooling
As a prominent player in the metal fabricators sector, DeepMould is at the forefront of integrating plastic injection tooling into its operations. By blending advanced metal fabrication techniques with sophisticated injection molding processes, DeepMould is able to offer comprehensive solutions that meet the complex demands of their clients. With a commitment to quality and innovation, DeepMould not only enhances productivity but also ensures that products are manufactured to the highest standards of excellence.
Commitment to Innovation
DeepMould's investment in cutting-edge technology—such as computer-aided design and precision machining—has allowed the company to streamline its plastic injection tooling processes. This commitment to innovation ensures that clients receive not only the best products but also the most efficient service.
Challenges in Plastic Injection Tooling
Despite the myriad benefits, plastic injection tooling does come with its challenges. Understanding these can help businesses prepare for potential obstacles:
- High Initial Costs: The initial costs of designing and creating molds can be substantial, which might deter some companies from utilizing this process.
- Complexity of Design: While the process allows for intricate designs, creating a mold that accommodates these complexities can be challenging and time-consuming.
- Material Limitations: Not all plastics are suitable for injection molding, and finding the right materials that meet all requirements can be tricky.
Future Trends in Plastic Injection Tooling
The future of plastic injection tooling is bright, with several trends likely to shape its evolution in the coming years:
Increased Automation
As technology continues to advance, the automation of processes within plastic injection tooling is expected to rise. This will enhance efficiency and accuracy, reducing labor costs and human error.
Sustainability Initiatives
With an increasing focus on sustainability, the development of bio-based and recyclable plastics will drive changes in plastic injection tooling. Manufacturers are likely to shift towards greener practices, ensuring environmental responsibility without compromising quality.
Integration of Smart Technologies
The integration of IoT (Internet of Things) and smart manufacturing technologies into plastic injection tooling processes is on the horizon. This connectivity will allow real-time monitoring and optimization, further improving productivity and reducing waste.
Conclusion
In conclusion, plastic injection tooling stands as a cornerstone of modern manufacturing, providing businesses with the ability to produce high-quality, consistent, and complex components efficiently. The benefits it offers to industries ranging from automotive to medical devices are undeniable. Companies like DeepMould are leveraging these advantages to enhance their operations and deliver exceptional products to their clients. As innovations continue to unfold in this arena, the potential for growth and improvement in plastic injection tooling is limitless, ensuring its relevance and importance in the manufacturing sector for years to come.