Understanding the Importance of an Injection Moulding Factory for Your Business
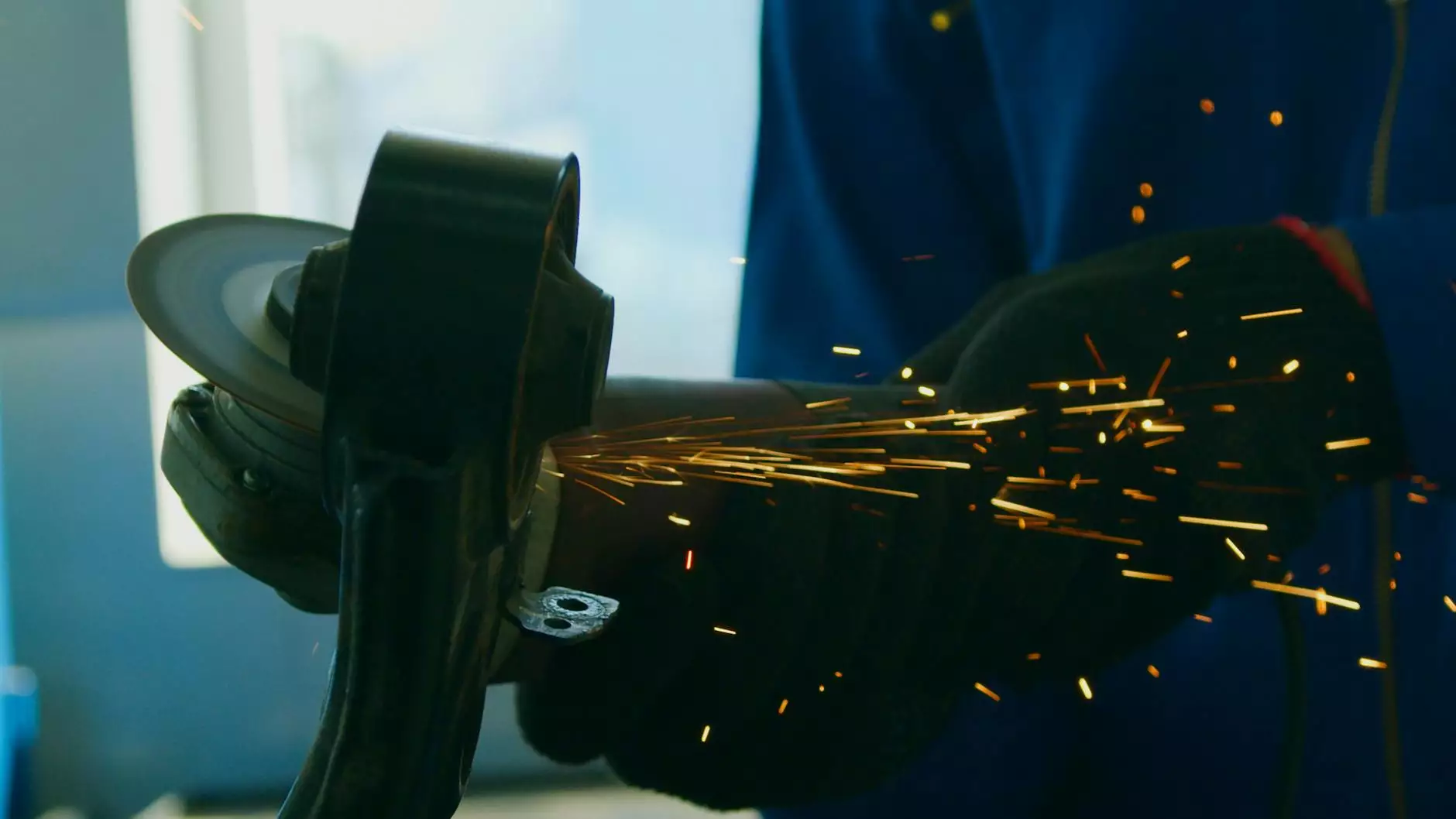
In the world of modern manufacturing, an injection moulding factory plays a pivotal role in the production of plastic components that are integral to various industries. This article delves deeper into the significance of injection moulding, its benefits, and how partnering with a quality injection moulding factory like DeepMould can enhance your business operations.
What is Injection Moulding?
Injection moulding is a manufacturing process used for producing parts by injecting molten material into a mould. It's widely utilized for producing plastic parts, but it can also accommodate metals and glass. The strength of this manufacturing technique lies in its ability to create complex shapes with high precision and repeatability.
The Process of Injection Moulding
The process involves several distinct steps:
- Designing the Mould: The journey begins with design, where engineers create a detailed and precise mould tailored for the required product.
- Melting the Material: The selected material, typically plastic resin, is heated until it reaches a molten state.
- Injecting the Molten Material: The molten material is then injected into the prepared mould under high pressure.
- Cooling and Solidifying: Once injected, the material cools and solidifies inside the mould, taking on its final form.
- Removing the Product: After cooling, the mould opens, and the finished product is ejected, ready for inspection and further processing.
Benefits of an Injection Moulding Factory
Turning to an injection moulding factory offers numerous advantages for businesses across various sectors, especially those specializing in metal fabrication.
High Efficiency and Scalability
One of the foremost benefits of injection moulding is its efficiency. Large volumes of identical parts can be produced rapidly without compromising quality. This scalability makes it an excellent choice for businesses looking to grow.
Cost-Effective Production
While the initial setup cost for mould creation can be high, the long-term savings on mass production make it a cost-effective solution. The low per-unit cost becomes more significant with larger orders, allowing businesses to maximize profits.
Precision and Consistency
Injection moulding offers exceptional precision in dimensions and properties, ensuring that every piece adheres closely to specifications. This consistency is crucial in industries where quality control is vital, reducing waste and rework.
Versatility in Material Use
An injection moulding factory can use a variety of materials—from standard plastics to advanced engineering thermoplastics. This versatility enables businesses to select the right material for their specific applications, leading to better-performing products.
Injection Moulding and the Metal Fabrication Industry
The intersection of injection moulding and metal fabrication is an emerging area of interest for manufacturers. While injection moulding is traditionally associated with plastics, it’s increasingly being used in the fabrication of metal parts.
Innovations in Metal Injection Moulding (MIM)
Metal injection moulding (MIM) combines traditional injection moulding techniques with metal powders to create high-density and complex metal components. This process allows the production of intricate geometries that are difficult or impossible to achieve through conventional machining methods.
Advantages of MIM
- Design Flexibility: MIM enables the production of complex shapes that can lead to innovative designs, providing businesses with a competitive edge.
- Reduced Waste: With MIM, there's less material waste compared to traditional machining, as parts are created near their final shape.
- Lower Production Costs: MIM can be cost-effective for high-volume production, as manufacturing costs can decrease significantly with scale.
Choosing the Right Injection Moulding Factory
Selecting the right injection moulding factory is crucial for your business's success. Here are key factors to consider:
Experience and Expertise
Look for a factory with a proven track record in the injection moulding process, particularly in your specific sector. Experienced manufacturers can offer insights and solutions that can greatly enhance your product quality.
State-of-the-art Technology
The injection moulding industry is constantly evolving with new technologies. Ensure that the factory utilizes the latest equipment and processes to guarantee high quality and efficient production.
Quality Control Measures
A reliable injection moulding factory should have stringent quality control protocols in place. This includes both in-process inspection and final product testing to ensure compliance with industry standards and specifications.
Customer Service and Support
Excellent customer service is essential. The factory should be responsive to inquiries, provide clear communication throughout the production process, and offer after-sales support to address any concerns.
Conclusion
In conclusion, the role of an injection moulding factory cannot be understated in today's manufacturing landscape. It offers unparalleled efficiency, precision, and versatility that can significantly benefit businesses involved in metal fabrication and beyond. By choosing a reputable partner like DeepMould, you can leverage state-of-the-art technology and expert knowledge to enhance your product lines and ultimately increase your competitive advantage in the market.
Call to Action
If you're looking to elevate your manufacturing processes, consider reaching out to DeepMould today. Let us help you harness the power of injection moulding for your business’s success!